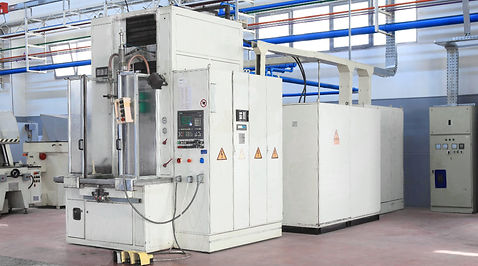
The Process in Önerler
In our company, there are a total of 6 medium and high frequency induction hardening machines for induction hardening process. All of our machines are of German origin and in different sizes and powers.
-
Treatment processes can be carried out in our high frequency machines up to 80 mm in diameter and 1000 mm in height.
- In our medium frequency machines, it is possible to harden gears up to 500 mm in diameter, 3500 mm in length and 3500 mm in shaft diameter and up to 5000 kg.
Thanks to the computer control in our induction machines, repeatability and traceability of products are ensured by automatically controlling all parameters such as energy, process time, cooling rate.
What is Induction Hardeninig ?
.Induction hardening is a rapid method in which the surface of the material is heated to high temperatures and then immediately cooled to give hardness to the material. In this process the entire surface or only the desired area of the piece can be hardened to the required depth. Since carbon or nitrogen enrichment of the material surface is not performed in this process, the hardness value obtained after the process is directly related to the carbon concentration of the material.
The working principle of the process is that electrical current is passed through a copper coil manufactured according to the material, and eddy current is generated and heated by the magnetic field generated on the material by this current. The hardness depth is controlled by the strength and duration of the applied current. The surface of the material reaching the austenitizing temperature is rapidly cooled with a special chemical to provide martensitic transformation, and the material hardens as a result of this conversion. Then the material can be tempered to give the desired hardness and/or reduce the stresses on the material.

Suitable Steels
Induction hardening can be applied to a wide range of products from steel to cast iron. There is no practical application since martensitic transformation cannot occur in steels with low carbon concentration. It is a method used only for surface hardening of low carbon steels which has been only subjected to carburizing and whose surface is enriched with carbon at the end of the process.
Potential Risks After Process
As induction consists of sudden heating and cooling processes, there are risks of waste and distortion. Because of the high hardenability of high-carbon, high-alloy steels, there is a risk of cracking and therefore the process parameters should be carefully calculated. During the design phase of the induction process, attention should be paid to geometric properties such as sharp corners, holes, etc. Otherwise, melting and cracking can be observed in these indicated regions. Casting cavities that can form on cast iron and on the surface of cast iron materials can cause melting and cracking during the induction hardening process.
Heat Treatment
BOSB Turuncu Cad. No: 12, 16120
Nilüfer/Bursa, TURKEY
+90 (0224) 242 43 10
+90 (0224) 242 43 11 (fax)
Steel Supply
Beşevler Sanayi Sitesi 26.Blok No: 6-15
Nilüfer/Bursa, TURKEY
+90 (0224) 441 97 13
+90 (0224) 441 46 15 (fax)